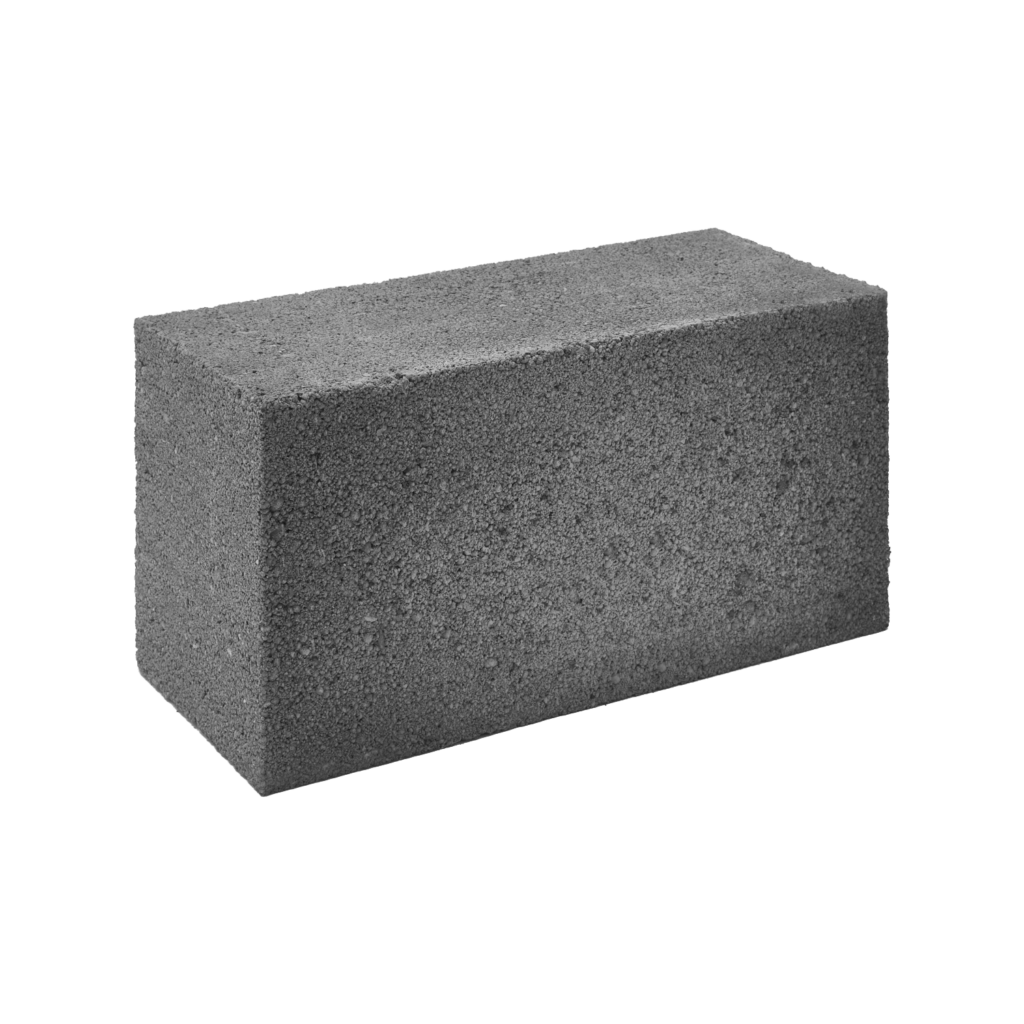
Lignalite 190mm Lightweight Block
Lignalite blocks provide combine ease of handling with thermal efficiency and are available in standard and paint finish grades.
Available in a 190mm block thickness, when compared to more slender walls, Lignalite blocks can be used to create greater spanning walls saving on vertical or horizontal supports.
Manufactured to BS EN 771- 3, Lignalite blocks are tough, durable and suitable for all types of buildings.
Block Gallery
Click an image to enlarge.
6 images
Block Benefits
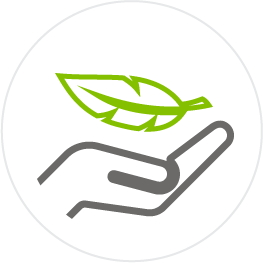
Light & Easy to Handle
Lignalite conforms to manual handling guidelines, which specify that each unit’s weight must not exceed 20kg when repetitive handling is needed.
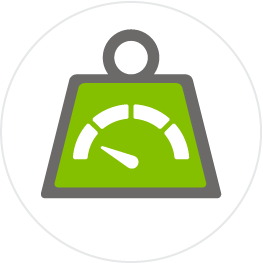
Low Self-weight
Lignalite is produced with a dry density of just 1030kg/m3. This results in walls that have relatively low self-weight, which places less load on the structure for a more economic building design.
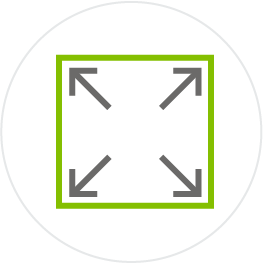
Maximise Panel Sizes
Using 190mm Lignalite blocks allows you to maximise the size of internal walls when compared to the use of slender blocks, such as those of 100mm and 140mm thickness. This benefit reduces the need for additional strengthening, such as that provided by wind posts or beams.
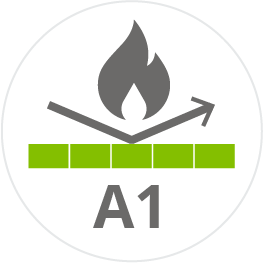
A1 Fire Rated
Blocks are non-combustible and make no contribution to fire, earning them a Class A1 rating.
Specification & Application
Block Standards
Lignalite blocks are BSI Kitemarked and approved to BS EN 771-3. They are Category 1 masonry units manufactured under a BSI certified Quality Management System, which complies with BS EN 9001.
Block Appearance
Lignalite is grey in colour with a close textured surface. Blocks required for direct paint application should be specified as ‘Paint Grade’
Block Application
Lignalite is suitable for the construction of both loadbearing and non-loadbearing walls in locations such as:
- The inner leaves of external cavity walls
- Internal walls, including fire break walls
- Separating walls
Block Specification
Face Size | 440mm x 215mm |
---|---|
Thickness | 190mm |
Mean Unit Strength | 7.3N/mm² |
Configuration | Group 1, solid blocks |
Dimensional Tolerances | Category D1 |
Net Dry Density | 1030 kg/m³ |
Thermal Conductivity | 0.37 W/mK at 3% moisture content (internal use) |
Airtightness: (m³/hr/m²)Painted on one face | 190mm blocks: 9.1 |
Airtightness: (m³/hr/m²)Painted on two faces | 190mm blocks: 4.0 |
Reaction to Fire | Class A1 |
Moisture Movement | <0.9mm/m |
Durability Against Freezing/Thawing | Frost resistance in accordance with PD 6697, Table 15. |
Weights & Pack Sizes
All weights are approximate and subject to normal variations in raw materials.
Table 1 – Concrete Block Weights and Pack Sizes
Face size | Thickness & block type | Unit weight (kg) | Laid weight inc. mortar (kg/m²) | No. of blocks per pack |
---|---|---|---|---|
440 x 215mm | 190mm solid | 19.1 | 210 | 32 |
(1) Unit weights are approximate and based on 3% moisture content by weight.
Sound Properties
Lignalite blockwork provides good levels of sound insulation between buildings and adjoining rooms. The Weighted Sound Reduction Index (Rw) values of various Lignalite wall constructions are shown in Table 2.
Table 2 – Sound Reduction Values
Weighted Sound Reduction Index: Rw, (dB):
No finish | Paint finish | |
---|---|---|
190mm solid | 45 | 51 |
(1) Sound insulation values are based on technical assessments and tests to BS EN ISO 140-3.
(2) Paint finish is based on emulsion paint and applied to one or both wall faces.
Fire Resistance
Lignalite blocks are rated as Class A1, in accordance with BS EN 13501-1:2007+A1:2009. A1 materials are completely non-combustible and make no contribution to fire.
The fire resistance periods of Lignalite loadbearing and non-loadbearing walls are shown in Table 3. The data is derived from the National Annex to BS EN 1996-1-2. The fire resistance of loadbearing walls is influenced by the proportion of the load on a wall and annotated in the National Annex as a ≤1.0 or a ≤ 0.6. The fire values presented are based on the worst loading case (≤1.0) and can therefore be safely used for all loading conditions.
The thicknesses shown are for masonry alone and exclude finishes. For the fire resistance of walls with finishes, refer to the Lignacite Design Guide – Fire Resistance.
Table 3 – Fire Resistance
Block type No finish | Non-loadbearing wall (criteria E1) | Loadbearing wall (criteria RE1) |
---|---|---|
190mm solid | 4 hours | 4 hours |
(1) Solid blocks are Group 1 units as defined in BS EN 1996-1-1.
Thermal Properties
The thermal resistance values (m² K/W) of Lignalite blocks are shown in Table 4.
Table 4 – Thermal Resistance Values
Thermal Resistance (m² K/W): 3% m/c | |
---|---|
190mm solid | 0.51 |
(1) 3% moisture content (m/c) should be used for protected locations, such as the inner leaf of external cavity walls.
Sustainability
Block Environmental Impact Management and Responsible Sourcing
Our manufacturing plants operate to a BSI certified Environmental Management System (EMS), which complies with ISO 14001.
Lignacite Ltd also meets the requirements of BES 6001 – Framework Standard for the Responsible Sourcing of Construction Products (Certificate No: BES 580823). This independently awarded Responsible Sourcing Certification confirms that our products have been made with constituent materials that have been responsibly sourced. This extends to organisational governance, supply chain management and environmental and social aspects, all of which must be addressed in order to ensure the responsible sourcing of construction products. Certification to BES 6001 will allow credits to be gained under environment assessment schemes such as BREEAM.
Block Energy Management
A BSI certified energy management system in accordance with ISO 50001 (Certificate No. ENMS 751020) is used to help manage energy use.
Compliance with ISO 50001 is a valuable tool in helping to manage energy use and includes the following outputs.
- A policy for more efficient use of energy
- Fix targets and objectives to meet the policy
- Use data to better understand and make decisions about energy use
- Measure the results
- Review how well the policy works and continually improve energy management
Design
Block Structural Design
The design of walls incorporating Lignalite concrete blocks should be in accordance with relevant design standards, including BS 8103 Part 2, BS EN 1996-1-1 and the requirements of the Building Regulations.
The 190mm Lignalite block enables the use of large panel sizes with reduced vertical or horizontal supports. Not only does this provide an immediate cost saving compared with the use of more slender walls, but it also improves the continuity of the blockwork construction process. As fewer structural supports are necessary, the number of connecting ties and movement joints is also reduced.
To illustrate the increase in masonry panel size that can be achieved using 190mm Lignalite concrete blocks compared to 100mm and 140mm thickness units, see the below example.
Comparison of panel sizes using 100mm, 140mm and 190mm (Lignalite)
For this comparison, the following assumptions have been made:
- Blocks have 7.3N/mm² compressive strength
- Mortar strength is Class/Designation M4/(iii)
- All edges are simply supported, e.g., with metal ties
- No dimensions are to exceed 50 times the wall thickness (BS5628-1 recommendation)
- Blocks conform to special category manufacturing control
- Walls are subject to a lateral pressure, e.g., wind load, WK, of 0.35 kN/m²
Block Movement Control
Vertical movement joints should be considered in accordance with masonry design codes and the recommendations of Published Document PD 6697, at 6.0 - 7.0 metre spacings. In areas of increased stress, such as above and below openings in external walls, the blockwork may need to be reinforced to restrain movement.
Block Wall Ties
Under normal conditions, wall ties should be embedded 50mm into the mortar on each leaf, staggered in alternate courses and spaced in accordance with the following.
Table 5 – Wall Tie Spacings
Leaf Thickness (mm) | Cavity Width (mm) | Horizontal Spacing (mm) | Vertical Spacing (mm) | Ties per m² |
---|---|---|---|---|
Less than 90mm | 50 - 75 | 450 | 450 | 4.9 |
Over 90mm | 50 - 150 | 900 | 450 | 2.5 |
Block Mortar
Generally, the mortar type for work above ground level should be designation (iii) / Compressive Class M4. Stronger mixes may be required if blocks are used below ground.
Table 6 – Mortar Mixes
Mortar Designation (as per BS 5628-3) | Compressive Strength Class (as per BS EN 1996) | Recommended mix proportions of materials by volume |
---|---|---|
(iii) | M4 | 1:1:5 to 6 - Cement:Lime:Sand. 1:5 to 6 - Cement:Sand with or without air entrainment. 1:4 to 5 - Masonry Cement:Sand (with non-lime filler). 1:3½:4 - Masonry Cement:Sand (with lime filler). |
(ii) | M6 | 1:½:4-4½ - Cement:Lime: Sand. 1:3 to 4 - Cement:Sand with or without air entrainment. 1:2½:3½ - Masonry Cement:Sand (with non-lime filler). 1:3 - Masonry Cement:Sand (with lime filler). |
Block Service Life
When properly constructed, the durability of walls built using Lignalite products will match that of traditional masonry and will fulfil their intended function for the life of the building in which they have been installed (typically 100 years).
The blocks themselves will require no maintenance. Maintenance for walls will normally include items such as the replacement of sealant in movement joints and at junctions / openings. Repointing for walls that are exposed to the elements may be necessary towards the end of its service life.
Site Practice
Block Surface Finish Recommendations
Direct Painting
A mist coat followed by at least two coats of emulsion will provide a good finish. The actual coverage will depend on the quality of the paint and how it is applied (e.g., brush, roller or by spray). Always ensure that each coat of paint has fully dried before any further layers are added.
Drylining
Standard plasterboard can be fixed using adhesive dabs or onto timber battens or metal studs.
Plaster
Dense plasters can be applied using either 1:1:6 cement: lime:sand or 1:4 ½ Masonry cement:sand or 1:5 ½ cement:sand and plasticiser.
Lightweight plasters should be used in accordance with the manufacturer’s recommendations. Suitable plasters include British Gypsum’s Thistle Hardwall.
Finishing coats include British Gypsum’s Thistle Multi-Finish.
Block Safe Handling
For detailed advice, refer to Lignacite’s Sitework Guide and the Material Safety Data sheet.
- Block packs may be stacked on firm and level surfaces to a maximum height of 2 packs. Consideration of handling equipment’s suitability for site terrain and safety limits should also be given. Hand-operated pallet trucks may not be suitable unless pallets specific for this purpose are used and loads do not exceed the limits of the pallet truck or its operator(s). Care should be taken when opening packs that are wrapped or banded to ensure that items do not fall or otherwise endanger persons handling the blocks or those nearby.
- CIS77 ‘Preventing injury from handling heavy blocks’ (Construction Industry Advisory Committee) and in accordance with the Manual Handling Regulations 1992 (as amended). This concludes that there is a high risk of injury to individuals who repetitively manually handle blocks in excess of 20kg. Where practical, mechanical handling equipment should be used to transport block packs to the area of work.
- Blocks should not be installed if the temperature is at or below 3°C and falling.
- Blocks should always be laid on a full bed of mortar and vertical joints solidly filled.
- For walls built fair faced, sample panels are recommended, which should be built prior to commencing block laying to serve as a benchmark for defining and specifying the quality of work required. Please note that for paint grade products, colour consistency is not guaranteed. It is advisable to view sample panels at a distance of about 3m from the wall in good natural light.
Product Resources
Take a look at our handy downloadable guides, designed to help you get the best from our concrete blocks.
1 of 4